Student-Manufactured Press Brake to Benefit Multiple Majors
Thursday, April 3, 2014
Ingenuity among students, faculty and staff across various majors at Pennsylvania College of Technology is resulting in a cost-effective initiative that will benefit the institution and its academic programs for years to come.
The college is in the final stages of manufacturing a press brake, a machine that efficiently bends sheet metal. The completed device will be employed for hands-on student work in several majors, including auto restoration, collision repair, welding, and automated manufacturing and machining.
“This project reflects the true nature of Penn College,” said David R. Cotner, dean of the School of Industrial, Computing & Engineering Technologies. “It’s inventive, hands-on and collaborative. The students in particular are enjoying a tremendous experience manufacturing a machine that will benefit several majors. I’m very proud of all the individuals who are bringing the press-brake idea to life.”
Keith H. English, instructor of automated manufacturing and machining, and Roy H. Klinger, instructor of automotive technology, proposed the press-brake initiative after collaborating on various tooling projects and identifying a specific need for the new automotive restoration technology associate-degree major.
“We consulted with several faculty, administrators and informed students and came up with a design that we felt would serve our purposes,” English said. “Commercial press brakes tend to have a limited opening, sometimes only an inch or two. Our brake was designed with a large opening of over a foot, allowing larger, more complex parts to be formed. It also will allow the installation of custom dies aimed specifically at auto restoration panel-forming needs.”
The press brake’s capacity is 7 feet in width, and it will generate 50,000 pounds of force, enough to bend 16-gauge steel.
Since last fall, students in English’s fixture design and fabrication classes have provided hundreds of hours of fabrication and machining time to craft the press brake. Industrial robotics students are working with John M. Good III, instructor of manufacturing and machining, to design the hydraulic circuit that will power the press brake. Those students are also designing and installing appropriate safety devices that will prevent unauthorized access while the machine is in operation.
In all, 25 students and six faculty members have been involved with the project. English credits Jason B. Miller, Mount Joy, a manufacturing engineering technology major, for the press brake’s initial design. Miller also performed the tungsten inert gas (TIG) welding required for the project.
“This is a very exciting project,” said Colin W. Williamson, dean of the School of Transportation & Natural Resources Technologies. “Sheet metal fabrication in automotive restoration is a critical skill, as many body panels are impossible to find. A brake of this size allows students to form large sections of sheet metal, capable of forming almost any large body panel. It would be a tremendous expense to procure one of this type and size if we would even locate one of this dimension.”
According to English, it would cost “in the range of $40,000” to purchase a press brake with a similar capacity. The price tag for the Penn College press brake is approximately $1,000, thanks to donated supplies and student labor.
“The savings to the college is tremendous with our students manufacturing it,” Klinger said.
Upon completion this summer, the press brake will be housed at the automotive restoration technology area, located in College Avenue Labs.
“Knowing that this will benefit many people, it feels good,” English said. “It seems worth all the hard work.”
For information about automated manufacturing and machining majors and other programs offered by the college’s School of Industrial, Computing & Engineering Technologies, call 570-327-4520.
For information regarding the automotive restoration technology program and other majors offered by the School of Transportation & Natural Resources Technologies, call 570-327-4516.
For more about Penn College, which is celebrating its Centennial throughout 2014, email the Admissions Office or call toll-free 800-367-9222.
The college is in the final stages of manufacturing a press brake, a machine that efficiently bends sheet metal. The completed device will be employed for hands-on student work in several majors, including auto restoration, collision repair, welding, and automated manufacturing and machining.
“This project reflects the true nature of Penn College,” said David R. Cotner, dean of the School of Industrial, Computing & Engineering Technologies. “It’s inventive, hands-on and collaborative. The students in particular are enjoying a tremendous experience manufacturing a machine that will benefit several majors. I’m very proud of all the individuals who are bringing the press-brake idea to life.”
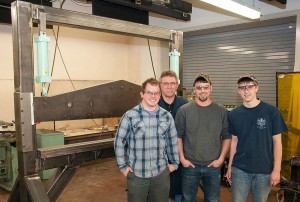
“We consulted with several faculty, administrators and informed students and came up with a design that we felt would serve our purposes,” English said. “Commercial press brakes tend to have a limited opening, sometimes only an inch or two. Our brake was designed with a large opening of over a foot, allowing larger, more complex parts to be formed. It also will allow the installation of custom dies aimed specifically at auto restoration panel-forming needs.”
The press brake’s capacity is 7 feet in width, and it will generate 50,000 pounds of force, enough to bend 16-gauge steel.
Since last fall, students in English’s fixture design and fabrication classes have provided hundreds of hours of fabrication and machining time to craft the press brake. Industrial robotics students are working with John M. Good III, instructor of manufacturing and machining, to design the hydraulic circuit that will power the press brake. Those students are also designing and installing appropriate safety devices that will prevent unauthorized access while the machine is in operation.
In all, 25 students and six faculty members have been involved with the project. English credits Jason B. Miller, Mount Joy, a manufacturing engineering technology major, for the press brake’s initial design. Miller also performed the tungsten inert gas (TIG) welding required for the project.
“This is a very exciting project,” said Colin W. Williamson, dean of the School of Transportation & Natural Resources Technologies. “Sheet metal fabrication in automotive restoration is a critical skill, as many body panels are impossible to find. A brake of this size allows students to form large sections of sheet metal, capable of forming almost any large body panel. It would be a tremendous expense to procure one of this type and size if we would even locate one of this dimension.”
According to English, it would cost “in the range of $40,000” to purchase a press brake with a similar capacity. The price tag for the Penn College press brake is approximately $1,000, thanks to donated supplies and student labor.
“The savings to the college is tremendous with our students manufacturing it,” Klinger said.
Upon completion this summer, the press brake will be housed at the automotive restoration technology area, located in College Avenue Labs.
“Knowing that this will benefit many people, it feels good,” English said. “It seems worth all the hard work.”
For information about automated manufacturing and machining majors and other programs offered by the college’s School of Industrial, Computing & Engineering Technologies, call 570-327-4520.
For information regarding the automotive restoration technology program and other majors offered by the School of Transportation & Natural Resources Technologies, call 570-327-4516.
For more about Penn College, which is celebrating its Centennial throughout 2014, email the Admissions Office or call toll-free 800-367-9222.
Photo by Craig R. Urey, student photographer